The Transformative Power of Precision Injection Molding in Metal Fabrication
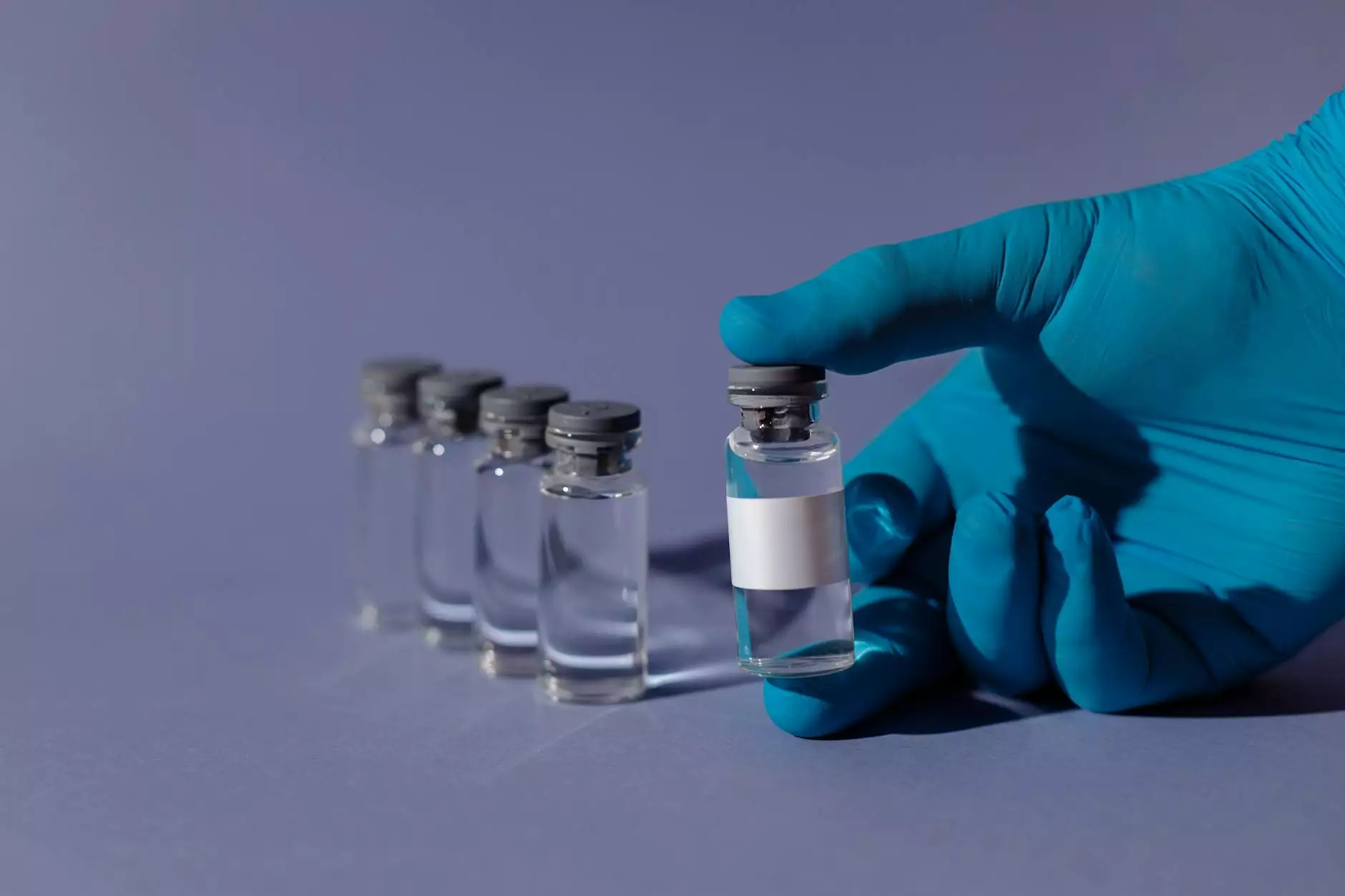
In today's competitive manufacturing landscape, precision injection molding stands out as a game-changing technique, redefining the standards in the metal fabrication industry. This article delves into the intricacies of this innovative process, examining its benefits, applications, and the future it heralds for manufacturers and consumers alike. Specifically, we will explore how businesses like DeepMould are at the forefront of this transformation.
Understanding Precision Injection Molding
Precision injection molding is a precise manufacturing process employed to create intricate parts by injecting molten material into a mold. This method is not limited to plastic alone; it can be adapted to produce high-quality metal components. The implications of utilizing precision injection molding in metal fabrication are significant, boasting enhancements in both efficiency and product quality.
How Precision Injection Molding Works
The process begins with the creation of a mold crafted to exact specifications. Molten metal—often aluminum or zinc—is injected into this mold under high pressure. As the metal cools and solidifies, it takes on the shape of the mold, resulting in a finished component with exacting dimensions.
The precision involved in this method allows for tight tolerances, a critical requirement in industries that demand high performance. The process can also produce complex geometries that traditional metal machining may find challenging or impossible to replicate.
Components of Precision Injection Molding
- Mold Design: A crucial step that directly influences the quality of the end product.
- Material Selection: Choosing the right alloy or metal is vital for achieving desired strength and durability.
- Temperature Control: Maintaining the optimal temperature throughout the process is essential to prevent defects.
- Injection Pressure: High pressure is key to ensuring that the molten metal fills the mold completely.
Advantages of Precision Injection Molding
The benefits of incorporating precision injection molding into metal fabrication are manifold. Not only does this method streamline production, but it also enhances the overall quality of the products. Some key advantages include:
1. Enhanced Efficiency
The automation of the injection molding process leads to faster production times. Manufacturers can produce large quantities of parts in a fraction of the time it would take using traditional metalworking methods.
2. Reduced Material Waste
Since molten metal is injected precisely into molds designed for minimal waste, manufacturers can significantly reduce the excess material typically associated with machining processes.
3. Superior Product Quality
The precision of the molds ensures that each part is made to exact specifications, resulting in high-quality components with fewer defects and a consistent finish.
4. Cost-Effectiveness
While the initial setup costs for precision injection molding may be higher than traditional methods, the long-term savings due to reduced material waste, faster production, and lower labor costs make it a more economical choice.
Applications of Precision Injection Molding in Metal Fabrication
The versatility of precision injection molding allows it to be applied across various industries. Some notable applications include:
- Aerospace: Producing lightweight, durable components that meet stringent safety and quality standards.
- Automotive: Creating intricate parts such as engine components and brackets with high precision for performance and reliability.
- Consumer Electronics: Manufacturing housings and frames that require complex designs and tight tolerances.
- Medical Devices: Ensuring that critical components meet the highest standards of hygiene and precision.
The Role of Technology in Precision Injection Molding
The integration of advanced technologies plays a pivotal role in enhancing precision injection molding processes. Technologies such as computer-aided design (CAD), computer-aided manufacturing (CAM), and advanced robotics contribute to the efficiency and accuracy of the molding operation.
1. Computer-Aided Design (CAD)
CAD software allows engineers and designers to create detailed digital models of the components to be manufactured. This ensures that every aspect of the design is accounted for before the molding process begins, reducing errors and streamlining the production cycle.
2. 3D Printing and Prototyping
Rapid prototyping technologies, such as 3D printing, can be used to create molds or even test components quickly. This not only speeds up the development process but also allows for immediate adjustments to be made before moving into full production.
3. Automation and Robotics
Automation in the injection molding process minimizes human error and increases consistency. Robots can handle the intricate tasks of part removal, quality inspection, and even the injection process itself, resulting in a far superior output.
Challenges in Precision Injection Molding
Despite its numerous advantages, precision injection molding is not without its challenges. Understanding these challenges helps manufacturers implement effective solutions to optimize the production process.
1. High Initial Costs
The initial investment for setting up precision injection molding systems can be substantial, dissuading some businesses from adopting this technology. However, firms like DeepMould demonstrate that the long-term benefits outweigh these initial hurdles.
2. Design Limitations
Although precision injection molding can create complex parts, there are still limitations in terms of the size and intricacy of the designs. Understanding these limitations during the design phase can prevent costly errors later in the process.
3. Material Selection Complexity
Choosing the right material for the job is crucial for achieving the intended performance characteristics. Different materials have unique properties that can affect the molding process and the properties of the finished part.
The Future of Precision Injection Molding
As manufacturing technology continues to evolve, the future of precision injection molding looks promising. Innovations such as machine learning, IoT integration, and smarter materials are on the horizon, all aimed at improving efficiency and product quality further.
1. Smart Manufacturing
The rise of smart manufacturing techniques, including IoT devices, will enable real-time monitoring and adjustment of the injection molding process, leading to enhanced quality control and predictive maintenance capabilities.
2. Advanced Materials
Research into new metal alloys and composites is ongoing, paving the way for lighter, stronger, and more durable components that can be produced using precision injection molding techniques.
3. Sustainability Practices
The focus on sustainability is increasing within the industry. Precision injection molding offers opportunities for recycling and reducing material waste, aligning with global efforts to promote eco-friendly manufacturing practices.
Conclusion: The Impact of Precision Injection Molding on Metal Fabrication
The advent of precision injection molding marks a significant milestone in the metal fabrication industry. By adopting this innovative method, businesses can achieve unparalleled efficiency, quality, and cost-effectiveness. Companies like DeepMould are leading the way, showcasing how precision molding techniques can revolutionize manufacturing processes, paving the path for future innovations.
As industries continue to embrace the benefits of this cutting-edge technology, the potential for growth and advancement in metal fabrication is immense. It is clear that precision injection molding will play a crucial role in shaping the future of manufacturing, fostering more efficient, high-quality production methods that cater to the needs of modern industries.